Rapid prototyping is often regarded as being synonymous with additive manufacturing (commonly termed 3D printing) technologies. However, a compelling case can also be made for CNC machining and injection moulding as rapid prototyping technologies, at least argues Stephen Dyson (pictured) of Telford-based specialist rapid prototyping provider Proto Labs.
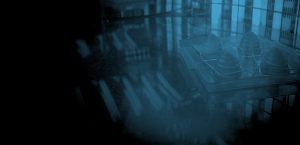
Increasingly, rapid prototyping is a strategic capability. Being the first to market with a new product or refinement confers a competitive edge, and being able to quickly develop prototypes gives an important advantage in that race to be first. And once earned, a reputation for innovation leadership tends to stick: customers will defer buying decisions until they have had a chance to see the offerings from those businesses with a track record of delivering market-defining products and product enhancements.
For certain projects, rapid prototyping is a management discipline. In the race to be first, there is no point having roadblocks or bottlenecks in key design and development processes. And the more strategic an end product is, the more important it becomes to make sure that prototypes and their designs do not loiter at the back of the queue.
But rapid prototyping is also a technology decision, and as rapid prototyping increasingly moves centre-stage in the push to be first to market, that technology decision is becoming increasingly important.
Put another way, the selection of the wrong prototyping technology can have a lasting and damaging effect on both time-to-market and product quality or reliability. This is because, in a world where rapid prototyping is often synonymous with the use of additive manufacturing technologies of various types, manufacturers are in danger of becoming overly reliant on it as a prototyping technology. Sure enough, 3D printing might well deliver a part that helps check form, function and fit, but where a project requires other critical attributes, such as suitability for pre-compliance testing or customer validation, other prototyping processes may be more suitable.
Prototypes manufactured using a standard 3D-printing process are produced undeniably quickly, but the resulting plastic parts may have poor strength. Stereolithography (SL) and selective laser sintering (SLS) technologies are processes that produce strong parts, but they are not always suitable for functional testing, and may provide limited data on manufacturability. In addition, parts produced through SL tend to become brittle over time, while the surface finish of parts produced through SLS tend to require additional aesthetic enhancement.
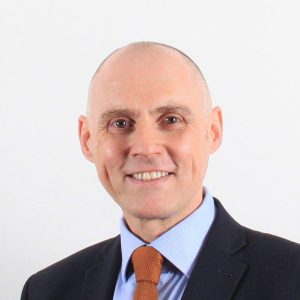
Rapid prototyping through direct metal laser sintering (DMLS) and fused deposition modelling (FDM) is generally regarded as a significant improvement in terms of physical strength, the resulting prototypes being made of various metals (in the case of DMLS) or industrial-strength resins (FDM). But as additive manufacturing processes go, FDM is quite slow and produces parts with a potentially unacceptable surface finish, while DMLS-produced parts can be expensive if requirements call for more than a handful of components. And again, indications of finished-part manufacturability are comparably limited.
In short, while additive manufacturing technologies are ideal for producing parts with extremely complex geometries that will permit the checking of form, fit and function, in many cases, post processing (such as CNC machining of certain surfaces) enhancements may be required to meet the needs of the project.
So what does that leave in terms of rapid prototyping technologies? The answer, perhaps surprisingly, is CNC machining and injection moulding; technologies that are often generally regarded as being mainstream production processes.
In both cases, the resulting parts will have the same physical properties and surface finish as the finished part, and will generally provide excellent indications of manufacturability. In short, if an important aspect of the overall development process involves testing the physical properties of parts, then a convincing case can be made for rapid prototyping through CNC machining and injection moulding technologies, especially if the prototyping process calls for small batches of components, as opposed to one-offs.
Furthermore, again in both cases, it is very possible for these technologies to be genuinely rapid. Both are capable of extensive digitisation, with the time taken to produce an injection-moulded part being further reduced by machining the requisite moulding tool from aluminium rather than steel. In short, coupling CNC machining and injection moulding as a prototyping technology may take a little longer than with additive manufacturing, but can yield vastly more useful data in terms of the conformance characteristics of the prototypes in question, as well as their manufacturability. Plus, the added cost is spread as the number of required prototypes increases.
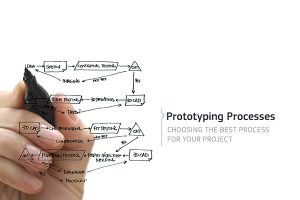
Even so, this is not to say that there is no place for additive manufacturing within a prototyping strategy. Of course not. It is simply that a well thought-out prototyping strategy is likely to be one that embraces several rapid prototyping technologies; additive manufacturing to start with, in order to provide initial data on form, fit and function, before moving to CNC machining or injection moulding as appropriate for subsequent rounds of prototypes. The acquired data will then provide the necessary confidence to invest in the CNC machining or injection-moulding process.
Ultimately, the decision process is more complicated than a policy of using only 3D printing technology. However, as rapid prototyping becomes an ever-more strategic capability, deciding which technology to employ is increasingly worth in-depth consideration. So, if an OEM discovers that its rapid prototyping provider cannot support digitisation together with CNC machining and injection moulding capabilities, then it could be time to look for another provider which does.
For further information www.protolabs.co.uk