Using Edgecam’s Waveform roughing strategy, a UK gear technology specialist has saved what it describes as an “astonishing 45 hours” – an entire week of milling production time – on a batch of 30 gears manufactured in hardened tool steel
Gibbs Gears, based at Stoke Mandeville in Buckinghamshire, predominantly works on low-to-medium volume runs of loose gears, gearboxes and assemblies, along with bespoke transmissions, and drive trains.
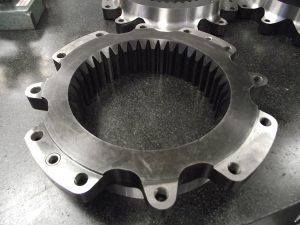
Managing director Reece Garrod says that the company typically manufactures orders of up to 200 gears for aerospace, motorsport, medical, subsea and commercial products: “Aerospace applications are largely for actuation, as part of the drive train mechanism to control flaps on wings. We produce cam and timing gears for motorsport, along with sequential gearbox and straight-cut crash gearbox assemblies for off-highway vehicles such as JCB and Caterpillar.”
Gibbs Gears also produces batches of up to 5000 fine-pitch gears between 0.3 and 1.25 module.
The company first tried Edgecam’s Waveform roughing strategy on a production run of 30 gears made from H13 tool steel, which had a Rockwell hardness value of between 53 and 58. Here, each standard milling operation on every gear would have taken two hours.
Technical manager Dominic Prinsloo explains that Waveform reduced those two hours down to just 29 minutes. He opted for a standard carbide cutter with an 8% step-over, a spindle speed of 6800 rpm and a feed rate of 2.8 m/min. “It meant that overall we saved an astonishing 45 hours of run time.”
Furthermore, Prinsloo says that the entire batch was completed using just one 16 mm diameter roughing end mill, which led to considerable savings on cutting tool costs. He feels the company could have pushed the CNC four-axis Matsuura VX1000 machining centre even harder, but chose to optimise it there, as it could run without supervision. “The operator was free to run a second machine, so again, that improved our overall efficiency.”
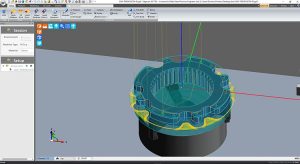
Gibbs Gears first became interested in Edgecam at the 2015 Southern Manufacturing exhibition in Farnborough. At that time, the company’s programming was all done at the machine, punching in G- and M-code. Edgecam now forms part of a three-pronged programming system. A small number of simple programs are still entered at the machine and programmed offline in ISO code, but Edgecam is used on around 60% of parts, driving a number of Doosan and Mazak turning centres, and four-axis Matsuura and Haas milling machines.
As well as reducing programming, set up and machining times, the software also comes into its own on controlling feeds and speeds, as Garrod explains: “We manufacture from a variety of metals including aviation grade stainless steels, carbon steels, case hardened and toughened tool steels, along with exotics such as Inconel and titanium, so Edgecam’s capability to let us ramp up feeds and speeds is proving invaluable.”
He also says that other shop floor operatives are keen to work with Edgecam: “We’ve recently started to use Edgecam on our AgieCharmilles EDM machine for wire erosion. That was at the request of the shop floor. They saw the benefits that Edgecam brings to other parts of the operation, and wanted to try it where we need a quick turnaround. Wire erosion accounts for around 10% of our business. We use it mainly on tooling, rapid tooling, jigs, fixtures and gauging, along with gear forms – especially for motorsport. But it’s growing in terms of gear technology, and where it’s allowable in the process we’ll erode gears, keyways and splines.”
Describing how Gibbs Gears uses the software, Prinsloo says that once he receives the customer’s STEP file – normally to finished size – he imports it into Part Modeler, Edgecam’s 3D modelling tool for quick and simple construction or modification of solid models, thus simulating a profile. “Then we’ll edit it to our tolerances for grinding, and revolve the profile again to make a finishing product which we can use for turning. We’ll load the stock model at this stage, and look at feature recognition.”
Edgecam is also used right at the start of an initial enquiry. “It’s now an important part of our quoting process,” says Garrod. “When customers provide us with a STEP file of the gears they want us to make, Edgecam gives us an accurate cycle time.”
Gibbs Gears is also working towards bringing in the PCI template on the planning board, which Garrod says will be particularly useful on two counts: firstly, to store common toolpath events in a ‘toolpath process library’ for re-use on other parts; and secondly to copy specific machining instructions from one part, and paste them into another. “This will accurately generate the feeds and speeds for whatever material we’re using.”
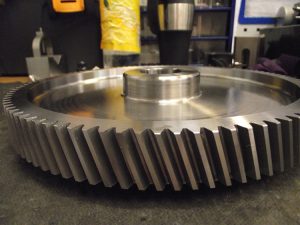
In conclusion, Garrod says: “We originally looked at Edgecam to help us progress with our ‘lean’ journey. KPIs showed that our biggest inefficiencies were coming in programming time, both for milling and turning, along with set-up and cycle times, and offline programming looked like the best way to overcome that. The fruit that’s been borne from investing in Edgecam is that those time losses have been eradicated.”
Gibbs Gears has comprehensive gear manufacturing capabilities, which includes the production of the following types of precision gears: spur and helical, spline shafts, gear racks, pinions, worms and wheels, spiral and straight bevels gears, gearboxes and gearbox assemblies, miniature and small gears, and bespoke gears to specification. The company works closely with companies, from concept to product realisation, and from technical support to full gear prototype and development.
For further information www.edgecam.com