Investment in a new machine from Worcester Presses is helping a Cannock automotive supplier win over £750,000 of new contracts.
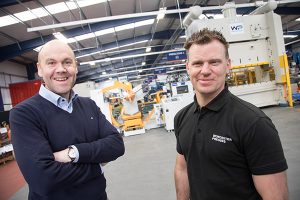
RSD Pressings, which supplies components for seats, sub-frames, cross car beams, bumpers and bodies, has installed a new GTX300 Chin Fong progression press and can now take on much bigger parts for tier-one customers and major car manufacturers.
Nearly £350,000 has been spent on the machine and a Tomac TLN4 coil line, with more than £100,000 of funding secured from Stoke-on-Trent and Staffordshire Grants 4 Growth, and the European Regional Development Fund. Three new jobs have already been created as a result of the investment and a further eight will be recruited over the course of the next 12 months once production starts on the projects already secured.
“The components we manufacture at our new facility in Cannock end up in millions of cars all over the world, including Aston Martin, BMW, Jaguar Land Rover, Nissan and Volvo,” explains operations director Daniel Burton.
“Worcester Presses came in, looked at our requirements and then developed a turnkey solution that involved the GTX 300, the latest HMI touch screen control and new Tomac TLN4 coil line which will increase our progression and coil feeding capabilities,” he adds. “This machine has doubled our bed size and already led to several new orders that we wouldn’t have been able to take on previously. There is still lots of capacity on it too, which means we are looking for even more new work.”
For further information www.worcesterpresses.co.uk