The workshops of the Llangollen Railway provide maintenance for the firm’s own rolling stock, as well as supporting other heritage railways around the UK and building brand new steam locomotives to order.
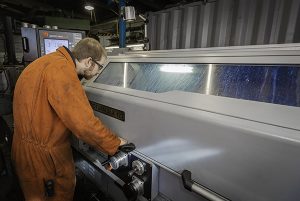
Like many such organisations, Llangollen Railway relies on donations, not only of cash and time, but also machine tools. However, when one particular project came up, the decision was taken to invest in new machinery in the form of an XYZ SLX 425 ProTurn lathe.
Llangollen Railway was tasked with the restoration of the iconic streamlined A4-class locomotive, Sir Nigel Gresley. In its life, the locomotive has had many overhauls, and the latest is taking place in full public view at the National Railway Museum in York by the Sir Nigel Gresley Locomotive Company Volunteers, except for its boiler, which has been stripped of its streamlining and transferred to Llangollen for refurbishment and re-certification. Part of the work involves replacing the boiler stays. As the boiler requires 296 of these stays of various lengths, with Whitworth threads at either end, an upgrade from manual turning was deemed wise.
The railway therefore took the decision to invest in an XYZ SLX 425 ProTurn lathe with 1.25 m between centres; a selection that is paying dividends as each boiler stay can now be machined complete in half the time that they previously took on a manual lathe.
“The ProtoTrak control makes life very easy as it guides you through everything; the ‘Traking’ feature is very handy and the ‘Do-One’ canned cycle feature in the control is extremely useful for machining features such as radii and chamfers,” says machinist Michael O’Toole.
For further information www.xyzmachinetools.com