As part of its quest for continued growth, excellence and product diversification, CMS Cepcor of Coalville has recently invested in the latest Creaform HandyScan3D from Measurement Solutions.
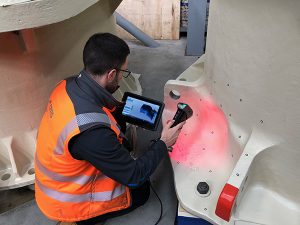
CMS Cepcor says it is Europe’s largest aftermarket manufacturer and supplier of stone crusher, screen and asphalt plant spare parts. The company provides its products and services globally to the mining, quarrying, demolition and recycling industries, exporting to over 100 countries.
To maintain its market status, operations director Chris Sydenham is constantly looking at new technologies and capabilities to drive efficiencies, customer satisfaction and product diversification.
This has been exemplified in recent years with around £7m invested in CNC, milling, turning, boring, slotting, grinding, drilling, welding, co-ordinate measuring and materials testing.
CMS Cepcor has made significant investments in three portable measuring and scanning arms during the last decade. However, the portability, and scanning capability in particular, resulted in the need to assess complementary technologies capable of increasing measurement efficiency
and usability.
“The Measurement Solutions team were able to visit our facility and demonstrate a device which is truly portable,” says Sydenham. “Although we design and manufacture in the UK, having the ability to take the HandyScan3D overseas is a major advantage, as the whole system is transported in a carrying case no larger than aircraft hand luggage. This gives us a whole new capability of scanning on-site, with the ability to send data back to the UK and begin the reverse engineering or inspection processes before our engineer has even boarded the plane home.”
Due to the scale of the components, the large field of view and scanning speeds generated by the HandyScan3D’s 14 laser lines far surpassed any other system considered, says the company.
For further information www.measurement-solutions.co.uk