Founded in 2016, Geneva-based Badeco SA manufactures high-precision components for the watchmaking industry.
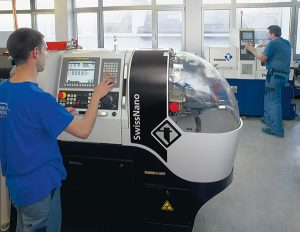
The company produces watch crowns, push-pieces, tubes, pinions, arbors, watch hands and parts for associated sectors, all on its in-house Tornos turning centres.
“We purchased two SwissNano CNC automatic lathes from Tornos as soon as we started our activities,” says managing director Stéphane Menoni. “Right from the start, they have proved to be particularly flexible and precise, while requiring minimum floor space.”
What was decisive, apart from the small footprint, was the flexibility of the SwissNano machines.
“Some high-precision components are manufactured in volumes up to 25,000 off, but it is also common practice to produce in small series or even perform one-off production,” says Menoni. “This means we can efficiently manufacture prototypes or spare parts.
“Since the space in our premises is restricted, we have installed the machines in an inverted position to gain additional space; this arrangement enables full access to the machining cell from the front,” he adds. “The machines are equipped with bar feeders and can be used for back machining as well as gear-cutting operations.”
Commissioning was quite easy, as Menoni affirms: “Just three days after the installation of the machines, the operator was fully familiar with set-up and operation. On the one hand, this was down to simplicity, and on the other it was the intuitive functions of the TISIS code editor. The latter is simply fantastic, since it allows program editing/transfer and tool selection, as well as machining process monitoring.”
For further information www.tornos.com