Burkhardt + Weber (B+W) has incorporated the stiffness and power of its heavy-duty MCX horizontal machining centres into a new, smaller model, the MCC 630. In so doing, the company says it has created one of the most rigid and powerful machines in its class for producing prismatic components weighing up to 1.5 tonnes (including the fixture). Availability in the UK and Ireland is through Geo Kingsbury Machine Tools.
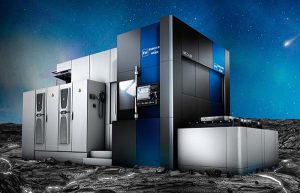
The four-axis machine (including C-axis rotary table), has twin 630 mm (optionally 630 x 800 mm) pallets and a nominal 1 cu m working envelope. External dimensions are 8 x 3.3 x 3.5 m.
B+W’s MCC 630 can deliver 1300 Nm of torque continuously if a 41 kW gear-driven spindle is chosen instead of a 30 kW/300 Nm motor spindle. There is a further alternative of a +45/-110° tilting spindle of identical power (also new), which adds a fifth CNC axis.
Spindle speed is up to 6000 rpm, optionally 10,000 rpm, while an ISO50 tool interface can be specified instead of the standard HSK-A100 with a tool clamping force of 45 kN. The tool changer serves a tool magazine with 64 pockets that can be doubled in size on request.
Productivity is promoted by a cutting feed force of 17.5 kN and 7 m/s2 acceleration to 60 m/min rapids in the linear axes, which are fitted with linear scales for feeding positional data back to the Siemens Sinumerik 840D sl control. B+W integrates a high level of Industry 4.0 monitoring and networking capability into its machines, offering data acquisition and communication for efficient production, process safety and timely maintenance.
For further information www.geokingsbury.com