As the inventor of the hydrodynamic bearing more than 100 years ago, Michell Bearings has spent the last century constantly developing its product range to meet the ever-changing needs of the company’s global customer base. The use of the latest production technology, decades of in-depth experience and the application of stringent quality systems, has resulted in the South Shields-based company gaining an impressive reputation in bearing design and manufacture for both the industrial and marine engineering sectors.
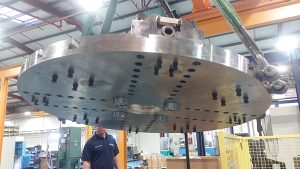
As the efficiency, reliability and longevity of any bearing depends largely on the quality of the methods used in its manufacture, Michell Bearings employs a wide range of CNC machine tools and advanced production aids.
The recent installation of a Hermle C60 UMT five-axis CNC machining centre prompted Chris Kemp, Michell Bearings’ manufacturing engineering manager to contact Tony Lewis of Thame Workholding with the intention of exploring ideas that would enable the company’s new acquisition to maximise its potential.
“As a designer and manufacturer of self-contained white-metal bearings and PTFE-faced hydrodynamic bearings, our products can be found in a range of challenging applications throughout the world,” states Kemp. “We have a long history of manufacturing bearings that withstand the test of time, and have products installed with 35 of the world’s navies on more than 300 vessels. Meticulous production and inspection methods ensure the quality of our bearings and help safeguard the global standing of the company.
“In accordance with our ongoing quest to enhance the company’s capabilities and further increase production efficiencies, we recently purchased a Hermle C60 UMT five-axis CNC machining centre with a capacity of 1200 x 1300 x 900 mm in the X, Y and Z axes. Our new machine tool allows the dynamic processing of workpieces up to 2000 kg in weight.”
With the aim of achieving the highest possible yield and looking to guarantee that the machine consistently met the demanding standards of precision at Michell Bearings, Kemp recently contacted Tony Lewis of Thame Workholding.
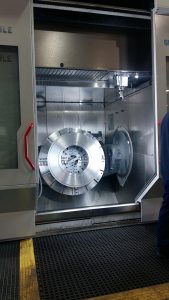
“After studying our new machine’s specification and capabilities, while also considering our objectives, we concluded that a work-holding arrangement, incorporating Thame Workholding’s Lang QuickPoint system and Samchully jaw boxes, would be ideal for our needs,” says Kemp. “By working together, Tony and I developed a system incorporating Thame Workholding’s products that has considerably reduced our new machine tool’s set-up and job change-over times, while greatly increasing its production availability. In addition to boosting efficiency, our new work-holding system’s ability to securely grip workpieces helps us to guarantee that the required levels of accuracy and surface finish are achieved on
a consistent basis.”
The work-holding arrangement conceived by Lewis and Kemp consists of several circular ‘slave’ plates that can be set-up offline. These slave plates have Lang QuickPoint studs attached to their bases and a series of QuickPoint plates that remain loaded on the machine table. The slave plates also feature T-slots that allow Samchully jaw boxes to be moved into position, tightened on to the workpiece, then centralised ready for machine loading.
On completion of a machining routine, the slave plate holding the finished part can be removed by crane, after which the next slave plate holding the new workpiece can be lowered into position. Upon quickly securing the new slave plate to the machine’s table, the next machining operation can begin.
The Hermle CNC machining centre’s spindle is able to move clear of the table, a useful capability that ensures the working area is completely unrestricted and accessible. As a result, completely unhindered crane loading is possible from directly above the machine table’s centreline.
According to Thame, the Lang QuickPoint system provides precise and repeatable mounting of fixtures and other elements on to machine tables, indexers, cubes, rotary tables and mill-turn machine tools. QuickPoint’s height of only 27 mm makes it the lowest profile zero-point-system currently available, says the company. Manual clamping is achieved with just one tightening screw (hydraulic or pneumatic clamping is also possible). The use of this simple and sturdy system allows a maximum pull-down force of 6000 kg.
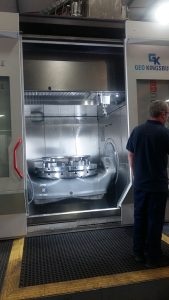
“The QuickPoint location system is based on four wedge bolts in the pallet that engage with four grooved locating bolts screwed to the vice or fixture,” explains Lewis. “The highly repeatable nature of QuickPoint guarantees that Michelle Bearings’ slave plates can be loaded with workpieces off-machine, then quickly and precisely attached to the Hermle machining centre’s table. Now, rather than wasting valuable time setting-up a workpiece when the machine is idle, then performing machining operations as subsequent activities, these processes are capable of being completed concurrently within the machine’s cycle time. Deploying this strategy can help deliver outstanding machining efficiencies.”
For further information:
www.thameworkholding.com
www.michellbearings.com