Colchester Machine Tool Solutions is exhibiting a complete range of turning machines with its distributor, Haberstroh GmbH, on stand 9D12 at AMB Stuttgart from 18 to 22 September 2018.
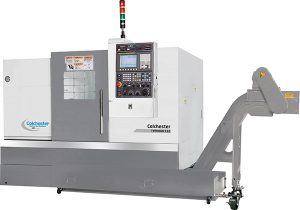
Alongside regulars such as the Colchester Student centre lathe and Harrison Alpha manual/CNC lathe, will be the new range of Colchester Typhoon CNC turning centres.
Recently launched in April, at the MACH exhibition in the UK, the Colchester Typhoon, which follows on from the Tornado range, has already created interest with orders now being taken.
Colchester offers Typhoon models as a choice of either linear (L series), or heavy-duty boxway (B series) turning centres, all available with variations of two-axis, C-axis, sub-spindle and Y-axis functions in a range of bar capacities to suit turning applications from 45 to 165 mm spindle bore.
Typhoon turning centres are fitted with the latest Fanuc Oi-TF control system with Manual Guide I, and are all manufactured with a one-piece cast-iron base featuring a 30° slant-bed design, giving a low centre of gravity and a better ergonomic design. Additionally, Typhoon models come with a large number of options for customers to get the best out of any complex machine tool requirements.
Paul Rushworth, Colchester Machine Tools’ sales director says: “AMB is one of the highest profile European shows in the machine tool calendar and, after considerable success in the UK, Spain, Russia and Austria already this year, we are looking to continue that trend.”
For further information www.colchester.co.uk