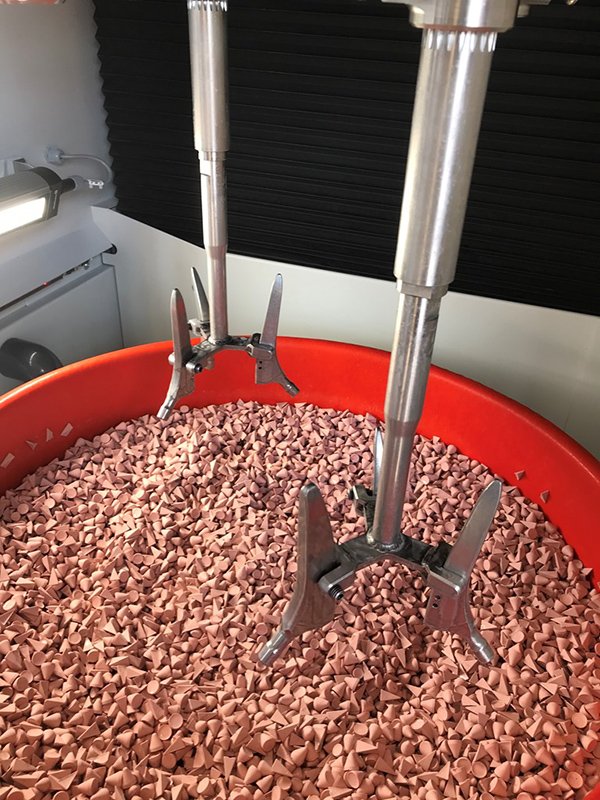
To ensure the optimal function of artificial hips in a patient’s body, certain surface areas on the hip stem must have different finishes. For example, the neck area of the stems requires a very smooth, polished surface. Recently, a manufacturer of precision components replaced a combined manual grinding/electropolishing operation with a fully automated two-stage mass finishing process. The Rösler R 4/700 SF drag finisher allows the simultaneous, precise finishing of 12 hip stems in one operation. This performance resulted not only in significant cost savings and lower cycle times, but in drastically improved quality and absolutely consistent finishing outcomes.
For 20 years, MBN Präzisionstechnik GmbH, located in the Austrian town of Pottendorf, has been specialising in the manufacture of machined precision components and assemblies. The company’s main focus is on the production of orthopaedic implants and surgical instruments made from titanium and stainless steel. MBN Präzisionstechnik, certified to DIN 13485, is not only equipped with ultra-modern machinery, including laser marking systems, but also has clean rooms for the coating and germ-free packaging of its products.
A particular challenge is the finishing of targeted surface areas on different hip stems. The company’s production is to a large extent automated and allows tracing the entire manufacturing chain, from raw material to finished product. Until recently, polishing of the neck area of the hip stems took place by a manual pre- and fine-grinding step, followed by an electropolishing process. This surface refinement operation was time-consuming, required a lot of manpower and was very costly. In addition, it was less than perfect with regard to consistency of the finishing results and general sustainability. Therefore, Thomas Müllner, general manager at MBN Präzisionstechnik GmbH, had been looking for an automated alternative for quite some time.
“Since only a precisely defined surface area must be polished, and a variety of different hip stem shafts must be processed, automating the surface finishing operation turned out to be quite challenging,” he says. “The first processing trials were undertaken by a supplier competing with Rösler. However, the results did not meet our quality standards.”
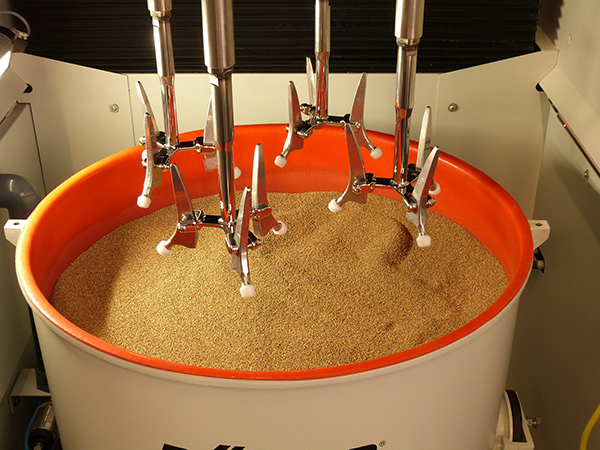
Based on the recommendation of one of MBN’s customers, the Rösler sales branch in Austria conducted further processing trials. This company is not only located nearby but also maintains a combined test and service centre. The Rösler experts decided to run the processing trials in a drag finisher. This proprietary mass finishing system allows the precise and targeted surface finishing of high-value workpieces with complex shapes. With the process parameters established, the operation runs without any variations, ensuring absolutely repeatable finishing results.
Says Müllner: “Rösler’s comprehensive know-how and experience from the job shop operation quickly helped to develop a two-stage process with drag finishing technology. The process, consisting of a wet grinding/pre-polishing step, followed by a dry polishing stage, produces a consistently high quality in surprisingly short cycle times.”
A major feature of the Rösler drag finishing technology is the vibratory motor mounted below the processing bowl.
“The vibration of the processing bowl ensures the optimal mixing of the processing media,” says Müllner. “This results in the absolutely homogeneous finishing of all relevant surface areas on the hip stems.”
In the end, MBN Präzisionstechnik chose a compact drag finisher, the R 4/700 SF model. This plug-and-play machine consists of a processing bowl with a diameter of 700 mm and a carousel with four rotating working spindles, each spindle allowing the mounting of three workpieces. The carousel and rotating spindles are equipped with separate drive systems so that the carousel and spindle speeds can be set independently of each other. Notably, the drag finishing machine comes with a second processing bowl. Using a lift truck it is possible to easily and quickly exchange the two bowls.

Prior to the grinding operation, the surface areas on the hip stems requiring no finish are masked, prior to the manual mounting of implants to special workpiece fixtures.
“For this purpose, we developed a clamping device that can be used for all stem types and sizes,” explains Müllner.
MBN’s team then attach workpiece fixtures (with secured hip stems) to the working spindles. Once the respective program has started, the carousel is lowered so that the rotating spindles are immersed in the processing media. For the wet grinding process, a mix of plastic media with different geometric shapes and a special compound are utilised. Carousel and spindles rotate at the pre-defined speed in opposite rotational directions. After about half of the cycle time – amounting to less than one hour – the rotational direction is reversed. This ensures that the neck areas of the hip stems receive an all-around perfect homogeneous finish.
For cleaning of the process water from the wet grinding process, MBN Präzisionstechnik purchased a Rösler semi-automatic Z 800 centrifugal process water recycling system. Recycling of the process water protects the environment and helps to reduce the finishing costs significantly.
For the polishing operation, a plant-based dry polishing media is utilised. At this process step, which requires a cycle time of well under 20 minutes, the processing bowl containing the finishing media is simply exchanged with the bowl filled with polishing media.
Müllner concludes: “With the automatic drag finishing process we could significantly improve the quality and consistency of the finishing results. At the same time, compared with our previous finishing operation, we could reduce the costs for grinding and polishing the hip stem neck by two thirds. Therefore, this investment will be amortised within a three-year period.”
For further information
www.rolser.com