Some 1.5 million parts are despatched every year from Worthing-based precision subcontract machinist Roscomac, a company that is achieving record on-time deliveries of 98%. The 85-employee company is driven by a philosophy of constant development and lean manufacturing techniques, supported by investment often exceeding £1m per annum.
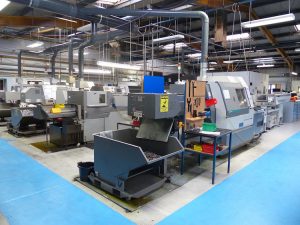
Says managing director Joe Martello: “We invest in automation and the latest production technologies, which helps to overcome the shortage of skills we require. However, it is so important that we still need to grow our own engineers through constant support and training, in order to maximise our ROI and improve how we support and what we deliver to customers.”
In the first six months of 2017, some £750,000 had already been allocated or spent, which included the installation of the latest Miyano BNE-51MSY multi-axis turn-mill centre. Two further CNC sliding head turn-mill centre machines have also been ordered and are soon to be delivered; again, like the Miyano, each is from Citizen Machinery UK. The two machines, a Citizen L20-VIII LFV (LFV featuring low frequency vibration cutting technology) and a top-of-the-range M16-V will bring the total Citizen installations to 14 machines as two earlier Citizen models are being sold.
“The levels of operational flexibility in the Miyano BNE has enabled us to significantly reduce machining times and, most importantly, improve overall productivity,” says cell leader Sean Keet. He explains that the new machine has replaced existing three-axis machines and outlines how a family of 10 aluminium parts has seen four previous turning and a separate milling operation reduced to just one turn-milling cycle. A bonus is that average total cycle times per part have been cut from 13 to just 2.5 minutes. Indeed, a further complex stainless steel component, which had three operations taking 11 minutes, is now reduced to a single 4-minute cycle.
The flexibility of the BNE-51MSY is key to what cell supervisor Warren Harris, responsible for the machine, is achieving. Specified with high-pressure coolant, Kid 80 bar feed, hybrid chuck and latest Wizard programming aid, the machine is capable of single-cycle cutting with three tools simultaneously overlapped at both ends of a workpiece.
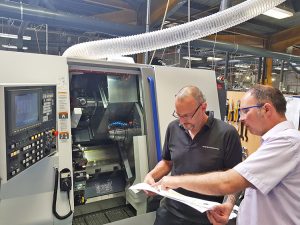
“The configuration of the three- and two-axis turrets gives us the flexibility to develop an application and room to add toolholders to overcome problems such as selective and controlled in-cycle deburring, for instance,” says Harris. “This saves us additional manual or further operational deburring tasks.”
He describes how the training given by Citizen Machinery helped in developing different approaches to setting the operational cycles: “We had an initial induction at our works and two of us were sent for programming at Citizen’s headquarters in Watford. Then, after two months, and adding to our own in-house experiences, further in-depth training was given.”
He maintains this helped to build a working relationship: “Even now, if we have a question or problem, we text or email the application team and they quickly come back to discuss the issue.”
The family-owned business of Roscomac was set up in 1976 on an industrial estate of 21 units owned by Martello’s father Fernando, who is still involved with the company. However, the company grew so fast that by 1999, subcontract production filled 20 of the 21 units.
The site was then sold and the current 43,000 sq ft factory was constructed on a 2-acre site in Worthing. Indeed, with planning permission granted, in 2018 a 3800 sq ft extension will be added and a complete new roof installed over the facility. As part of the drive to maintain quality (AS9100 approved) and improve the working environment, climate control has recently been installed across the factory which maintains a constant 22°C.
Today, some 50 CNC machine tools are installed, including 13 Citizen CNC sliding-head turn-mill centres and a large 104 pallet FMS. There are also 17 machining centres in the plant involved in supplying the medical (20% of £6.5 million turnover) aerospace (12%) vacuum technology, oil and gas, motion and hydraulics, and nuclear sectors. A number of different materials are machined, ranging from plastics through to alloy steels such as Inconel. Parts are also exported to France, Germany and the Czech Republic.
Martello adopts the same working relationships with machine tool and equipment suppliers as most of his long-term customers maintain with him and his team. This means his key equipment is only bought from a small group of ‘partnership’ suppliers in which Citizen Machinery UK (formerly NC Engineering) has participated since 1990. In that time the company has installed 16 sliding-head and two Miyano fixed-head turn-mill centres, plus the two Citizen machines now on order.
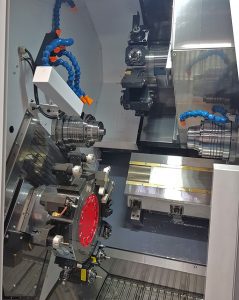
“Our relationship with customers is built on support, quality and on-time supply,” says Martello. “Suppliers such as Citizen are in the same category, with the added capability to be consistent in providing us with leading technology developments that will keep us competitive and enable us to properly service our customer base. The coming installation of the Citizen L20-VIIILFV is a classic case in providing a level of technology which will take us into another sphere of manufacturing that few competitors will be able to match for some time to come.”
Current batch sizes at Roscomac range from 30-off to thousands of parts, while a prototype and process development/design support service is also offered. In addition, the company maintains stock for key customers, which provides a major benefit when tailoring batch work to economic quantity levels and helps achieve a 98% on-time delivery target. As a result, this statistic has been improved over the last four years from levels of around 60%. Indeed, with productivity targets now running at 200% of man-hours available, this has been aided by setting up five overlapping shifts during the week in order to maximise machine utilisation and spindle uptime.
To help maintain momentum of production with the workforce, every 3 months employees are taken aside to a conference room for presentations made by Martello and key staff members for a business update which encourages open communication. These sessions are backed-up with live screens around the factory area showing current workloads and status of workflow, and target and actual delivery dates achieved.
“This keeps everyone aware and involved,” he concludes. “It also draws comment and constructive suggestions for improvement.”
For further information www.citizenmachinery.co.uk