On 23 March, Being Brunel, a new museum that brings together the world’s most significant Brunel collection at Brunel’s SS Great Britain in Bristol, UK, opened to the public.
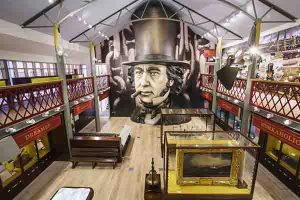
To assist with its development, metrology specialist Renishaw has supported the museum since 2015 and was the founder member of the Being Brunel Corporate Club, created to enable local companies to support the development of the new museum. As well as sponsoring Being Brunel, Renishaw has made a video contribution to one of its galleries. The new museum celebrates the life and legacy of Isambard Kingdom Brunel.
For further information www.renishaw.com