Almost 10 years ago, JCB CEO Lord Anthony Bamford had a vision for educating the next generation of engineers.
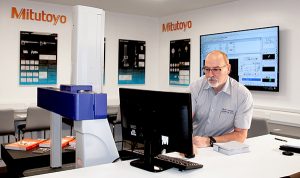
This inspirational spark led to the internationally recognised yellow goods manufacturer establishing the JCB Academy in 2010. To ensure education is vocationally suitable for future generations of engineers, the JCB Academy is supported by metrology expert Mitutoyo.
At the centre of the metrology department at the JCB Academy is a Crysta-Plus M443 CMM that is connected to a 60” wall mounted monitor. The manual Crysta-Plus CMM with temperature compensation offers the facility everything from simple dimensional to complex form measurement on a small footprint 400 x 400 mm table. Utilising the latest MCOSMOS CMM software, learners can evaluate the dimensional precision of components and test pieces. By connecting the CMM to a large monitor, teaching staff can conduct practical demonstrations to learners in a classroom environment.
The vision of Lord Bamford is certainly starting to pay dividends for the future of UK manufacturing and, in particular, the future of JCB.
“As a company, JCB has thousands of employees and there is natural staff wastage of approximately 350 people every year through retirement and other factors,” says Graham Rowley, team leader for technical delivery. “The academy is now generating future recruits, while giving prospective employees a strong grounding in engineering.”
With regard to the service, support and expectations placed upon Mitutoyo, Rowley concludes: “We’ve never had an issue with Mitutoyo; the support is excellent. In terms of how quickly they respond to either an email or a call, there is always somebody on hand with the correct technical information. Furthermore, if we ever need on-site technical assistance, there is always someone available to come to our facility, usually with same-day call-out support.”
For further information www.mitutoyo.co.uk