Precision Technologies International Ltd has recently installed a Klingelnberg Höfler Viper 500K universal gear grinding machine at its Tamworth headquarters; the first machine of its type in the UK.
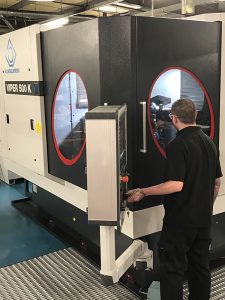
Technical sales director at Precision Technologies Colin Palin says: “In order to expand our capacity, meet both current and anticipated demand, and further increase our in-house capabilities, we recently investigated the available high-end, external/internal gear and spline grinding machines. Having judged several suitable machines against our demanding wish list, we came to the conclusion that the Klingelnberg Höfler Viper 500K met and in many ways exceeded our expectations.
“For instance, thanks to the logical operating system, our staff quickly became skilled in the machine’s use,” he continues. “The Viper 500K is now producing the required high quantities of ground gears with complex geometries for use in automotive and motorsport applications, as well as other equally challenging areas.”
Klingelnberg Höfler’s Viper 500K gear grinding machine, as purchased by Precision Technologies, is designed to accommodate component diameters of up to 500 mm. Multiple-wheel technology is featured, making the machine suitable for the production of small to medium-sized batches.
The configuration of the machine allows users to change the grinding technology by quickly swapping-out the grinding wheel, the grinding wheel flank and the dressing wheel. An optional internal gear grinding arm allows re-tooling and conversion from external to internal gearing work.
According to Palin, “the help of Mark Maurice, the owner of UK Klingelnberg Höfler agent Micronz, was invaluable when specifying the machine and ensuring trouble-free installation and operator training”.
For further information www.micronz.co.uk