A recently signed annual ‘Preferred Partnership Agreement’ has been signed between Glasgow-based Walker Precision Engineering and Seco Tools UK.
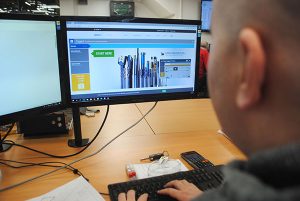
The agreement, with its emphasis on continuous improvement and best-practice methods to help WPE increase productivity levels, reduce operational costs and optimise machining processes, provides the company with preferential and priority access to a range of Seco’s technical consultancy services, including: on-site and off-site technical support; turnkey and process improvement; documented cost reduction (DCR) programmes; custom tool design, manufacture and supply; STEP (Seco Technical Education Programme) training courses; regular updates on new technologies and process developments; and new tooling and service introductions and upgrades.
To ensure that the agreement is focused, proactive and maintains momentum, regular monthly planning and quarterly review meetings with key personnel from WPE and Seco are scheduled.
Within the first few months of the agreement being signed, the partnership was delivering results, most notably with the machining of a complex precision chassis part-manufactured by WPE for a defence industry customer. Working in partnership with Seco’s product and technical staff, and employing process improvement strategies and a focused DCR programme, WPE has been able to reduce cycle times for this part by 40%.
At one of the planning meetings, Seco presented an overview on My Pages – the company’s digital portal that provides customers with access to Seco product information, cutting data, previous purchase history and test reports. Benefits include the ability to quickly and reliably find the most appropriate tool for any specific application, which is achieved by searching the on-board SUGGEST database and selecting specific component characteristics, machining priorities and machining strategies that will be employed.
For further information www.secotools.com