Derby-based Tidyco, a supplier of hydraulic and pneumatic products to the UK rail industry for over 40 years, has invested £150,000 in state-of-the-art tube-bending machinery. The CNC tube-bending machine includes a programmable robotic measuring arm coupled with machine-to-machine (M2M) technology. Tidyco says that the investment will allow it to rationalise outsourcing activity so as to provide cost-effective solutions to its client portfolio.
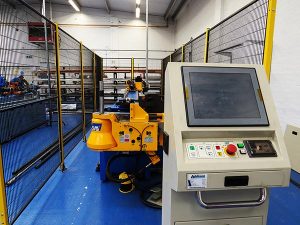
The expansion contributes towards Tidyco’s commitment to smart manufacturing, addressing topical industry 4.0 subject matters.
Importantly, the company fully supports the Government-fuelled Industrial Strategy and Midlands Engine initiative whereby the family-owned business believes that ongoing investment will contribute towards manufacturing growth throughout the region. The new tube bender was part-funded by the University of Derby’s Invest to Grow initiative, with equipment being procured from Addison Saws and other local suppliers. Former Mayor of Derby, John Whitby, officially opened the manufacturing plant expansion.
Phil Mason, production director at Tidyco, says: “As a business, Tidyco is committed to a long-term growth strategy whereby continuing investment in additional manufacturing equipment forms part of overall critical success factors. The addition of a tube-bending facility will enable the company to supply customers with products in a much faster, accurate and cost-effective manner, while empowering new and existing staff working with our quality-control procedures. Ultimately, the investment further bolsters opportunities regarding new market penetration.”
Additional tube-bending capabilities include: a tube shaper measuring arm; full reverse engineering functionality; proficiency in bending most tubes from 8 to 50 mm; and STEP file conversion.
For further information www.tidyco.co.uk