Hypertherm, a manufacturer of industrial cutting systems and software, has released Design2Fab 6, a major update of its sheet-metal layout software for HVAC duct, mechanical, kitchen, industrial roofing and other specialty fitting layouts.
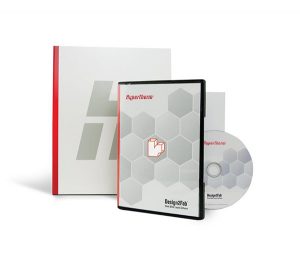
The new version is the most significant Design2Fab update since the software was acquired in 2004, and features an entirely new interface and tools that include a modelling engine for 3D geometric renderings. Better graphics, fluid movement and real-time updates are just a few of the benefits end users will see. Other improvements include easier dimension entry, an unlimited number of zones, easy arrangement of fittings with drag and drop functionality, ProNest nesting software integration, and more.
Engineered to reduce the time it takes to develop and lay out flat patterns, Design2Fab allows users to create both HPGL and DXF output formats: a plotter can be deployed to print an HPGL layout for manual cutting, or a CNC cutting machine to produce fittings from DXF files. In addition, prior to CNC cutting, users can export DXF files to ProNest, ProNest LT or ProNest LTS nesting software for optimal material utilisation.
Current Design2Fab users with an active software subscription can upgrade to the new version at no additional charge and continue to receive unlimited technical support, as well as other benefits.
For further information http://kb.hyperthermcam.com