With the acquisition of its long-standing software partner Comara GmbH, tooling expert Walter is reinforcing its decision to strive for further growth in the digital sector.
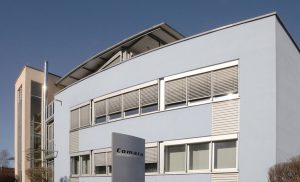
As Walter AG president Mirko Merlo, states: “This is a key strategic step towards expanding our digital portfolio and further developing our company towards Industry 4.0.” Acquiring Comara constitutes the next logical step
in Walter’s development from product to process partner, he adds, and now to digital process partner. Comara will remain an autonomous operation with separate products and its own retail arm.
For further information www.walter-tools.com