The Mitsui Seiki J350G jig grinder has an accuracy of ±0.0007 mm and a U-axis infeed range of between -3 and +50 mm to support continuous automatic grinding of multiple features, plus a variety of hole sizes and contoured shapes, with a single grinding wheel. Available in the UK from 2D CNC Machinery, the machine uses the Mitsui Advanced Programming support software, G-MAPS, which facilitates quick setting of wheel data, has a simple input screen and enables wheel and grinding conditions to be monitored (including hole location and position tolerances). There is also an analogue display for simple commands using switches and dials.
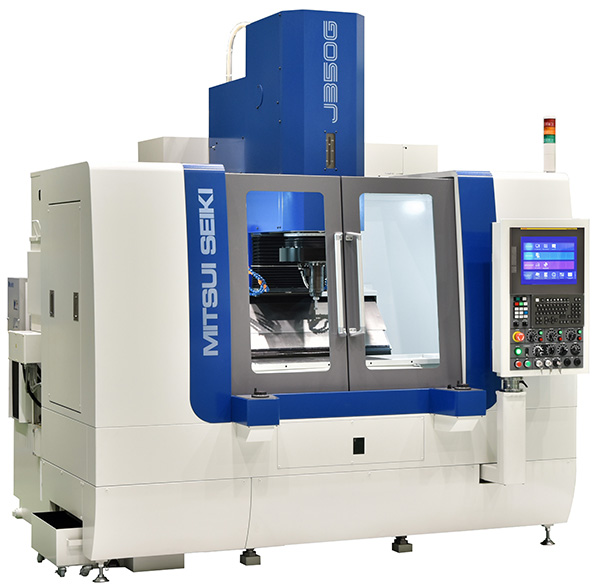
The J350G provides four specification options for high-frequency spindles covering the speed range from 9000 to 45,000 rpm, plus an ultra-fast air turbine of 175,000 rpm.
Both the left- and right-hand slideways are V-F flats, while the Y axis for spindle-head motion is V-V flat shaped. All bearing surfaces are hand scraped for positioning accuracy and repeatability. In addition, and included as standard following a partnership with Heidenhain, custom-built positioning scales for the X, Y and Z axes further extend accuracy potential.
The machine’s working range in the X axis is 500 mm, while Y-axis saddle traverse is 300 mm and the maximum distance from the 700 x 350 mm table, which has a maximum 350 kg load, is 450 mm. Z-axis quill travel is 100 mm with 95 mm ‘chopping motion’ available up to 200 cycles/min. W-axis travel is 300 mm. Further performance parameters include planetary motion speed at 5 to 300 rpm, and a grinding infeed stroke U-axis that extends from
-3 to +50 mm.
For further information www.2dcnc.co.uk