In engineering, a lot of focus is centred on complex systems and assemblies. Every manufacturer has a signature approach, or systems that help to define a brand. However, from a logistics point of view, every component is of equal importance. A shortage of a single, small bolt over an entire assembly can cause a production shutdown. Optimas, a global industrial distributor and service provider of C-class components, employs fastener experts on the ground at its partner manufacturing facilities to combat this issue.
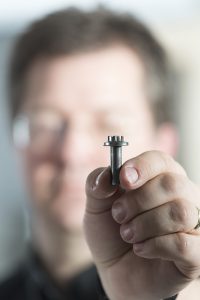
“The first step of any fastener relationship must be to gain familiarity with the customer’s operations,” states Ian Larkin, customer application engineer at Optimas. “Past experience in an industry can be important here, but leading manufacturers will enact varying approaches to achieve a finished product, so gauging specific customer requirements is important. Hence the advantage of having a fastener expert on the ground. In contrast, someone operating off site would not be able to reach the level of understanding required to accurately address specific fastener issues.
“As a fastener partner, we have to fit an ‘ideal standard’,”
he continues. “We are working with big global customers who are driven to succeed, so we have to respect current processes and enhance the component policy to the specific requirements of the manufacturer.”
The easiest way to gauge these requirements is during a line walk. An Optimas expert will travel the entire production line looking at points of use, while asking basic questions to see what can be tweaked or possibly improved. This way, the expert can meet key figures on the line, while also taking a focused approach to tackling fastener problems on the ground.
“We don’t want to tear up the customer’s rulebook, but if we can point out a cost saving or alternative option to production staff, we will do so,” says Larkin.
A good example of the benefits this strategy can provide to manufacturers is highlighted by one particular Optimas customer in the US.
“We noticed a washer was being added to a flange screw even though it wasn’t particularly necessary,” says Larkin. “These washers were identified at multiple points of use, so we posed the question to the assembly team. It turned out that during the design of the product, the head engineer had requested the inclusion of washers to improve the aesthetic of the overall product. We were able to demonstrate that the washers were unnecessary for the application, and as a result, delivered an annual cost saving of $30,000.
“You can utilise engineering expertise as part of a sales function, but it also adds value to our customers. By making sure that we don’t make presumptions, we start an open relationship with the customer in close proximity. This builds trust and lessens the impact of implementing new methodologies. By getting involved with the product and seeing how it is used, people on the ground can get a deeper insight into possible solutions.”
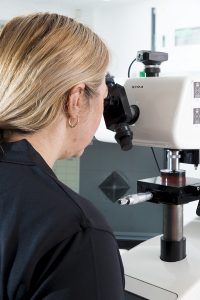
Another customer application engineer at Optimas, Gerry Abraham, adds: “A key aspect of integrating with a manufacturer’s operations is responsiveness. Such businesses work to exacting timeframes in all aspects of their work, whether full scale production or prototyping a new product. Fastener suppliers who simply supply components can leave manufacturers with the impression that if a component problem arises, they alone must solve the issue. Optimas aims to differentiate itself by working together with purchasing, design and engineering teams to aid problem solving.
Abraham says that one project comes to mind, which was in relation to design engineering activity for a new diesel engine. A bolted joint for the turbo mounting was backing off during testing. As a result, the turbo itself was coming loose, producing excessive noise in operation. The manufacturer approached Optimas for a solution.
“We connected the customer with a number of suppliers to help rethink the situation. The customer trialled three or four recommended locking-type fasteners to replace the problem part, before selecting a preferred option. Ultimately, we wanted to give the customer choice and a chance to improve performance, so they could be confident in the part going forward.”
Another key element in providing an integrated approach is cross-departmental communication, as engineering program manager Chris Sterner, points out: “By starting this dialogue from the beginning, efficiency and response is improved. In addition, close contact means that specific fastener solutions can be enacted across multiple projects. Open dialogue regarding each other’s projects allows wider implementation of identified solutions, instead of starting from scratch every time a potential problem arises. By standardising solutions, you also deliver cost and efficiency benefits.”
Consistent presence is clearly important for these customers. Optimas tries to breed familiarity by being present at design reviews, which is a lot more beneficial to the manufacturer than simply being on the end of a phone. It also allows Optimas to share solutions, as each fastener problem solved allows the company to convince these varied groups within a business that it can be trusted to deliver.
“Providing guidance on fasteners affects the activities of the purchasing, design, engineering and assembly teams – so being able to balance the requirements of each of these groups is paramount,” says Sterner. “Regular face-to-face contact is the optimum method, helping to build relationships between teams and delivering a fast response. Ultimately, a fastener expert must communicate across each department to achieve the perfect balance.”
Becoming a fully integrated fastener expert means taking the emphasis on component knowledge away from the manufacturer. Manufacturers therefore are not required to brush up on standard parts, availability, material standards or overall usage – enabling time to be spent on other areas of the business.
“One story really fits this philosophy,” says Sterner. “An Optimas expert was asked to demonstrate some fasteners that were mentioned during a customer meeting. As he didn’t have these samples readily available at the meeting, he took pictures of the fasteners that were installed on his own car. He even took out a number of fasteners from the vehicle so he could share samples with the customer and demonstrate their usage. While quite an extreme approach, it was certainly effective in demonstrating the solution to the customer.
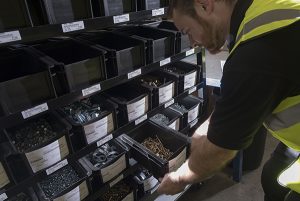
“The capabilities of the service also go a long way,” he continues. “Our access to failure mode analysis and full technical studies means we can provide exact answers to tackle fastener application issues. If we don’t have an answer ready for the customer immediately, this capability means we can react as fast as possible with a high technical proficiency. If it’s a unique problem, as fastener experts we can also learn from similar experiences, so the benefits of shared knowledge are also available.”
Fasteners are the only assets on a production line that are used uniformly, but with engineering typically focusing on landmark innovations, the emphasis upon them can be diminished. As a fastener expert, challenging this preconception is all part of the job.
“Fasteners may be the most inexpensive components that a manufacturer utilises on a production line, but they are one of the most critical,” concludes Sterner. “A lack of fasteners will shut down production just as much as complicated components, so we must demonstrate to our customers that the expertise we deliver can provide reliable service, no matter the challenge.”
For further information https://global.optimas.com