Built in 1903, the Welshpool and Llanfair Light Railway served communities along the winding valley that joined the mainline at Welshpool. This narrow-gauge railway allowed livestock, coal and timber to be transported easily, as well as providing a passenger service until the early 1930s. The line operated until 1956 when British Rail deemed it uneconomic.
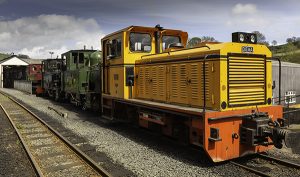
A regular steam-hauled public service once again returned to the line in 1963 when a group of enthusiasts took on the challenge of making it into a successful tourist attraction. Key to that success was the retention of two original locomotives and the acquisition of rolling stock from railways both in the UK and Europe. Now almost 120 years old, this historic collection requires regular maintenance and care, which is where the railway’s engineering workshop comes in to its own.
A little bit of catching up was required as the first maintenance workshop was not built until 1968 and the locomotives lived outside in the elements until 2000. An extension to the workshop in the 1980s saw the development of the machine shop, with machine tools being ‘begged, borrowed or stolen’ from supporters of the railway. Things improved in the 1990s when a Heritage Lottery grant allowed some additional machines to be purchased, but when mechanical engineering manager Richard Featherstone joined the railway in 2016 he recognised an adequate, but not ideal situation.
“We had a lot of manual machines and work on them was laborious, and given that we rely on some skilled volunteers, time is at a premium,” he explains. “What we needed was bigger and faster milling and turning capacity that also had to be user-friendly to cater for the skills and work we have.”
An appeal for funds went out and, as a result, the railway was able to order two machine tools from XYZ, an SMX 4000 bed mill and an SLX 425 ProTurn lathe. These machines have made an immediate impact on the way that Featherstone is able to support the maintenance of the engines. One example involves spark arrester plates for the smoke boxes, which are made up of a sandwich of stainless-steel plates and mesh held in place by 28 M6 screws.
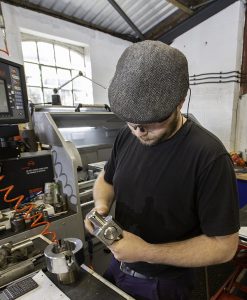
“The M6 drilled and tapped holes would traditionally have been marked out, centre popped and manually drilled, then adjusted by the fitters for assembly,” says Featherstone. “We now machine them on the SMX 4000 and every hole is in the right place; the time savings are significant.”
Similarly, the SLX 425 ProTurn lathe is generating major benefits for Featherstone and his team of volunteers. Each of the couplings between the engines and rolling stock has an adjusting nut which features an 11/4 4TPI round thread form. A batch of 15-off has been manufactured by a semi-skilled volunteer in an afternoon on the SLX 425. Previously, using manual machines, this task was a week’s work. For traceability, these parts are then put on the SMX 4000 and etched with the relevant details. Again, this operation would previously have been done by hand with letter and number punches.
“Maintenance and refurbishment is a continuous process here as the engines and components are subject to an aggressive environment; we are either boiling things or burning things,” says Featherstone. “For example, after every 28 days of being under steam we have to replace/rework the two fusible plugs in each boiler. These are bronze plugs with a 99.9% purity lead core. Their job is to act as a failsafe if water levels drop in the boiler – the lead melts and the flame is doused. Making these plugs was a black art as they feature a taper thread, which must be accurate, and a specific length as four complete threads should be showing on the inside of the firebox, a situation complicated by the fact that the female thread is occasionally re-tapped and opened-up.”
Today, this operation is a straightforward procedure as the program can be called up on the ProtoTrak control of the SLX 425 and offsets adjusted to instill confidence that accurate parts will be produced first time. Again, with the focus on availability of labour and time, with Featherstone currently being the only full-time member of staff in the workshop, these fusible plugs used to take a skilled-man four hours to produce a pair. In contrast, a pair of plugs can today be machined in under 15 minutes.
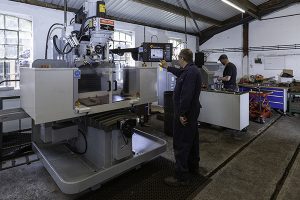
At present, programming is done at the machine by Featherstone; he is then happy to hand over the operating of the machines to semi-skilled volunteers, although this situation should improve when he recruits an additional full-time machinist. One feature that Featherstone is particularly enthusiastic about on the SLX Lathe is the TRAKing facility, which allows him to use the handles to move through the program, while remaining in full control.

“I love the TRAKing feature as you know you can back off if you have any uncertainty about the tool path,” he says. “That said, using step-by-step instructions on the ProtoTrak control, it is so easy to get things right first time.”
The Welshpool and Llanfair Light Railway is always
looking to recruit skilled engineers on a voluntary basis. Any expressions of interest can be made by calling the railway on 01938 810441.
For further information www.xyzmachinetools.com