When the KTR Group ordered new machine tools to reduce processing times, the power transmission specialist also opted for new workholding technology from Hainbuch. The Rheine, Germany facility of KTR was aiming to generate significant improvements in set-up times and the subsequent manufacturing process.
“Several machines were due to be replaced after reaching the limit of their service life,” explains production manager Günter Schleyer.
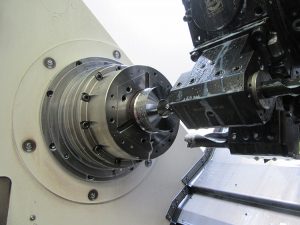
“Therefore, we re-examined the clamping requirements. The important questions for us were how to position ourselves in the future and how do we increase flexibility? Among other things, we use machine tools for both series runs and single-item production. Here we were at a crossroads. On one hand, we required a specialised series production solution and, on the other hand, we needed a fast, flexible cell for the single parts.”
The company took a Torok manual chuck with a base plate, a clamping head and a mandrel as part of a trial phase. For KTR, the overall time saving was extremely important.
Says Schleyer: “We needed to know how the system would perform under everyday conditions. We had questions like whether the Torok was rigid, and would it meet our practical requirements? Could we organise our set-up more efficiently? And of course, holding forces and repeatability were highly significant.
“Practical experience had shown us that conventional jaws were out of the question,” he continues. “For our coupling manufacturing, parts are machined at high cutting speeds. Cams and bores are milled and drilled, so we have a wide variety of chip shapes that must not impair the function of the clamping devices. Also, the solution should be practically self-cleaning. Needless to say, the implementation of the Torok manual chuck on one of the milling machines passed the test with flying colours. With these findings, the green light was given for working together with Hainbuch.”
For further information www.hainbuch.com